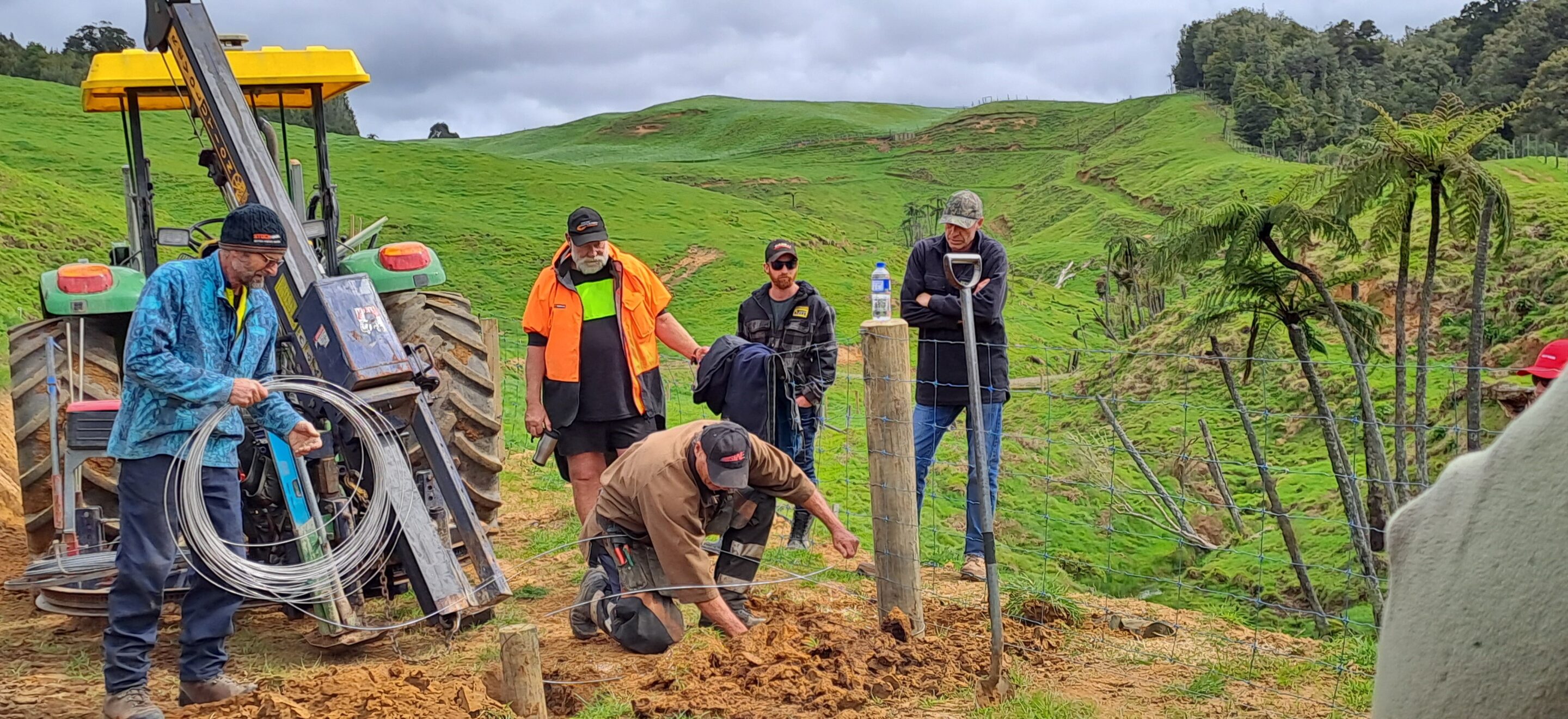
Many businesses wonder why they should train staff. Common reasons we hear for not training staff in the use of plant and equipment, or how to stay safe whilst working for the company include:
‘As soon as they know enough, they’ll be off, contracting on their own, after all my effort.’
‘Nah, it costs too much, they’ll figure it out.’
‘They told me they could do it.’
‘My staff aren’t worth it’.
‘It’s common sense!’
‘A bit of pain will teach them, right?’
Many workplace accidents are happening as workers don’t wish to say, ‘I’m not sure I can do that task’, or they don’t want to let you down, so will give it a go – sometimes with serious outcome.
Powerful Benefits of Employee Training & Development
Trained staff can do a job well and safely, and have pride in the job they do.
Training also:
- Increases employee performance
- Creates a stronger workforce
- Boosts motivation and engagement
- Expands knowledge sharing
- Fosters innovation in the workplace
- Improves company processes
- Creates a stronger business brand to clients
- Aligns with organisational goals
So, who is legally responsible for ensuring you have the correct training and supervision for your task on site?
Under the Health and Safety at Work (General Risk and Workplace Management) Regulations 2016 (the GRWM Regulations), a person conducting a business or undertaking (PCBU) must ensure, so far as is reasonably practicable, the information, training, instruction, and supervision provided to workers is suitable and adequate.
EXAMPLE FROM THE COURTS WorkSafe v Progressive Meats Ltd [2022] A 17-year-old worker operating a brisket cutter suffered partial amputation of his thumb, index finger, middle finger, and ring finger on his right hand. The injured worker was trained to use the machine by a co-worker who started on the same day as him. The co-worker demonstrated how to use the machine with one hand. The Judge convicted Progressive Meats on the grounds that, while the company had comprehensive safety and training systems in place, and was driven by the need to maintain safe procedures in all areas, it had not ensured adequate instruction, monitoring and supervision of workers. Progressive Meats was ordered to pay a fine of $280,000 and reparations of $48,000 to the injured worker. |
OFFENCE | INDIVIDUAL WHO IS NOT A PCBU OR OFFICER (EG A WORKER OR OTHER PERSON AT A WORKPLACE) | OFFICER OF A PCBU OR AN INDIVIDUAL WHO IS A PCBU (EG SELF-EMPLOYED) | ANYONE ELSE (EG AN ORGANISATION THAT IS A PCBU) |
Section 47 (reckless conduct in respect of duty that exposes any individual to whom that duty is owed to a risk of death or serious injury or serious illness) |
5 years in prison or a $300,000 fine, or both | 5 years in prison or a $600,000 fine, or both | $3,000,000 fine |
Section 48 (failure to comply with a duty that exposes an individual to a risk of serious injury, serious illness or death) |
$150,000 fine | $300,000 fine | $1,500,000 fine |
Section 49 (failure to comply with a duty) |
$50,000 fine | $100,000 fine | $500,000 fine |
Failure in this duty could be costly if serious harm were to occur – not just to you but also to the worker and family of the worker harmed.
What Information, Training, Instruction and/or Supervision should you cover?
Different work activities can require different levels of information, training, instruction, or supervision. Certain work activities require higher levels of training or supervision for workers and others in the workplace to remain healthy and safe. This includes remote or isolated work – i.e. your typical rural fencing job. You must engage with workers when making decisions about procedures for providing information and training to workers.
You must ensure, so far as is reasonably practicable, those who carry out work of any kind, use plant of any kind, or deal with a substance of any kind that is capable of causing a risk in a workplace:
- either have adequate knowledge or experience of similar work so they are not likely to cause harm to themselves or other people, or are supervised by someone who has the relevant knowledge and experience, and
- are adequately trained in the safe use of all plant, objects, substances, or equipment the workers are, or may be required, to handle, as well as all personal protective equipment (PPE) that the workers are, or may be required, to wear or use.
To work out what training (which includes the provision of information or instruction) or supervision you should cover, think about:
- The nature of the work carried out by the worker – e.g., what is the worker being asked to do? What is your workplace like in general?
- The nature of the risk associated with the work at the time the supervision or training is provided – e.g., what kind of risks are there?
- The control measures implemented in relation to the work being undertaken – e.g., what control measures are there already?
Consider:
- What your workplace is physically like – is it a quiet office, a busy workshop, a construction site, an outdoor environment, areas with lots of workers and members of the public nearby?
- What does your work involve – what machinery, equipment, PPE, and substances are used? What are the control measures in place?
- Your workers – e.g., what is their skill level and depth of experience regarding the known work risks?
Using this information, work out what skills, knowledge and experience your workers will need to work safely. This includes what information and training is required for dealing with emergencies.
Now work out what training, instruction, information, or supervision will be needed for workers to gain the skills, knowledge, or experience to work safely.
When the Training, Instruction or Supervision should occur
Work out when training/supervision will be required and how you will set aside enough time for this to occur (given the nature and risks involved in the work).
For example:
- Will new inexperienced workers be intensively supervised until they are shown to be competent to carry out the tasks unsupervised?
- Will new inexperienced workers be comprehensively trained for all tasks they may need to carry out in one go, or will they be trained/supervised on a task-by-task basis as needed?
- Will experienced workers only be supervised for new tasks for the first time? Think about how you will alert supervisors/trainers/workers when specific training/supervision is required before starting certain tasks. Think about how you can alert workers when certain tasks require training/ supervision – e.g., will you have warning signs on machinery or at workstations?
You must ensure, so far as is reasonably practicable, that the training and information provided is readily understandable by any person it is provided to. Trainers and supervisors of workers should be competent. They can be in-house or from external organisations.
Think about the best method of delivering training, instruction, or supervision. Consider your workers’ age and experience, their first language, any cultural differences, and the potential level of understanding of the workers.
For example, if some of your workers find it difficult to read, information or training may need to be provided orally, or through pictures or demonstrations. They may also need to be supported by a buddy or
supervisor.
Key considerations:
- What level of experience / competence your trainers or supervisors need to have.
- If your workers have previous experience with the work.
- If your workers have poor literacy or English as a second language.
- If your workers learn better one-to-one or in a group.
- If the training/instruction should be paper, audio-visual, or computerbased (including using tablets or smartphones).
- If there are relevant formal qualifications your workers could obtain (e.g., unit standards from NZQA).
- How you will get your workers to show they understand.
- How you could provide daily reminders of safe work practices (e.g., SOPs, posters or flashcards summarising the key points kept at workstations, and toolbox meetings) once the formal training is completed.
- If your workers can follow plant and machinery manuals.
- Workplace Approved Code of Practice (ACOPs) for tasks – have these available and read them.
How to tell the providers of the Training/Instruction/Supervision what must be covered
Think about how to tell supervisors/trainers/workers what the training should always cover, or how supervision needs to be carried out.
Think about how you can tell:
- Supervisors: what they need to do (e.g., will you have documented procedures?)
- Trainers: what training is required during new worker inductions and for certain tasks (e.g., will you have documented training procedures or checklists of points to be covered during training?).
FINALLY, you must ensure that your workers have signed:
- Relevant Safe Operational Procedures
- Read through the Workplace Risk Register
- Completed Competency Checklists
Training is valuable – teams grow and learn together. Make training part of your business and stay safe out there. Ask your advisor for help accessing resources, or connecting with trainers.
Luck runs out but safety is good for life.
Take care out there team.
Article written by Debbie
www.ruralsafe.co.nz
Published in Business, Health & Safety, Environment in WIRED Issue 71 / December 2023 by Fencing Contractors NZ